Sistemas de Lubrificação Centralizada: A Solução Eficiente para Manutenção Industrial
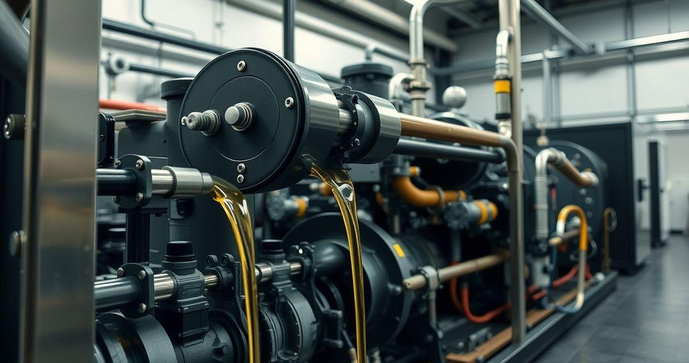
Por: Victória - 26 de Abril de 2025
Os sistemas de lubrificação centralizada desempenham um papel crucial na manutenção de máquinas e equipamentos industriais. Ao otimizar a distribuição de lubrificante, esses sistemas garantem que todas as partes móveis recebam a proteção necessária, aumentando a eficiência e a durabilidade dos equipamentos. Neste artigo, exploraremos as vantagens, o funcionamento e os tipos de sistemas de lubrificação centralizada, além de dicas para sua manutenção adequada.
Vantagens dos Sistemas de Lubrificação Centralizada na Indústria
Os sistemas de lubrificação centralizada têm se tornado uma escolha popular em diversas indústrias devido às suas inúmeras vantagens. Esses sistemas são projetados para fornecer lubrificação eficiente e consistente a várias partes móveis de máquinas e equipamentos, o que resulta em uma série de benefícios significativos. A seguir, abordaremos as principais vantagens que esses sistemas oferecem.
Uma das principais vantagens dos sistemas de lubrificação centralizada é a eficiência operacional. Com a lubrificação automatizada, as máquinas recebem a quantidade exata de lubrificante no momento certo, eliminando a necessidade de lubrificação manual. Isso não apenas economiza tempo, mas também reduz o risco de erro humano, garantindo que todas as partes móveis sejam lubrificadas adequadamente. A eficiência na lubrificação contribui para um funcionamento mais suave das máquinas, resultando em menos paradas não programadas e maior produtividade.
Além disso, a redução de custos é uma vantagem significativa. Sistemas de lubrificação centralizada permitem o uso otimizado de lubrificantes, evitando desperdícios. Com a lubrificação precisa, as máquinas operam de maneira mais eficiente, o que pode levar a uma diminuição nos custos de energia. Além disso, a manutenção preventiva se torna mais eficaz, pois a lubrificação adequada reduz o desgaste das peças, prolongando a vida útil dos equipamentos e diminuindo a necessidade de reparos dispendiosos.
Outro benefício importante é a segurança. A lubrificação manual pode ser uma tarefa perigosa, especialmente em ambientes industriais onde as máquinas estão em operação. Com um sistema de lubrificação centralizada, o risco de acidentes é reduzido, pois os operadores não precisam se aproximar das partes móveis das máquinas para aplicar lubrificante. Isso não apenas protege os trabalhadores, mas também minimiza a possibilidade de danos aos equipamentos, que podem ocorrer durante a lubrificação manual.
A consistência na lubrificação é outra vantagem crucial. Sistemas de lubrificação centralizada garantem que todas as partes móveis recebam a mesma quantidade de lubrificante, independentemente da localização ou do acesso. Isso é especialmente importante em máquinas complexas, onde algumas partes podem ser difíceis de alcançar. A lubrificação uniforme ajuda a evitar pontos de atrito e desgaste desigual, resultando em um desempenho mais confiável e duradouro.
Além disso, a facilidade de monitoramento é uma característica que não pode ser ignorada. Muitos sistemas de lubrificação centralizada modernos vêm equipados com tecnologia de monitoramento que permite aos operadores acompanhar o nível de lubrificante e o desempenho do sistema em tempo real. Isso facilita a identificação de problemas antes que se tornem críticos, permitindo uma manutenção proativa e evitando paradas inesperadas. A capacidade de monitorar a lubrificação também ajuda a garantir que os lubrificantes utilizados sejam adequados para cada aplicação, como o Lubrificante industrial apropriado, que pode ser selecionado com base nas necessidades específicas de cada máquina.
Outro aspecto a ser considerado é a redução de contaminação. Sistemas de lubrificação centralizada minimizam a exposição do lubrificante ao ambiente, reduzindo o risco de contaminação por sujeira, poeira e outros contaminantes. Isso é especialmente importante em indústrias onde a limpeza e a pureza dos lubrificantes são essenciais para o desempenho adequado das máquinas. A contaminação pode levar a falhas prematuras e a um aumento nos custos de manutenção, portanto, a proteção oferecida por esses sistemas é um benefício significativo.
Por fim, a flexibilidade dos sistemas de lubrificação centralizada é uma vantagem que merece destaque. Esses sistemas podem ser adaptados para atender às necessidades específicas de diferentes tipos de máquinas e processos industriais. Com a capacidade de personalizar a configuração do sistema, as empresas podem garantir que suas operações sejam otimizadas para o máximo desempenho e eficiência.
Em resumo, as vantagens dos sistemas de lubrificação centralizada na indústria são numerosas e impactantes. Desde a eficiência operacional e a redução de custos até a segurança e a consistência na lubrificação, esses sistemas oferecem soluções eficazes para os desafios enfrentados nas operações industriais. Ao considerar a implementação de um sistema de lubrificação centralizada, as empresas podem não apenas melhorar a performance de suas máquinas, mas também garantir um ambiente de trabalho mais seguro e produtivo.
Como Funciona um Sistema de Lubrificação Centralizada
Os sistemas de lubrificação centralizada são projetados para fornecer uma lubrificação eficiente e controlada a várias partes móveis de máquinas e equipamentos industriais. Esses sistemas são essenciais para garantir o funcionamento adequado e a durabilidade dos equipamentos, reduzindo o desgaste e a necessidade de manutenção frequente. Neste artigo, vamos explorar como funciona um sistema de lubrificação centralizada, detalhando seus componentes e o processo de lubrificação.
Um sistema de lubrificação centralizada é composto por vários componentes principais, que trabalham em conjunto para garantir a distribuição adequada do lubrificante. O primeiro componente fundamental é a bomba de lubrificação, que é responsável por pressurizar e distribuir o lubrificante para os pontos de lubrificação. A Bomba de lubrificação pode ser elétrica ou manual, dependendo do tipo de sistema e das necessidades específicas da aplicação. As bombas elétricas são mais comuns em sistemas automatizados, pois oferecem maior precisão e controle na distribuição do lubrificante.
Após a bomba, o lubrificante é transportado através de uma rede de tubulações. Essas tubulações são projetadas para conduzir o lubrificante até os pontos de lubrificação, que podem incluir rolamentos, engrenagens, e outros componentes móveis. A escolha do material e do diâmetro das tubulações é crucial, pois deve ser compatível com o tipo de lubrificante utilizado e capaz de suportar a pressão gerada pela bomba.
Os sistemas de lubrificação centralizada também incluem distribuidores, que são dispositivos que dividem o fluxo de lubrificante em várias saídas. Esses distribuidores podem ser ajustáveis, permitindo que a quantidade de lubrificante enviada a cada ponto de lubrificação seja controlada de acordo com as necessidades específicas de cada componente. Isso é especialmente importante em máquinas complexas, onde diferentes partes podem exigir diferentes quantidades de lubrificante.
Uma vez que o lubrificante chega aos pontos de lubrificação, ele é aplicado diretamente nas superfícies de contato das peças móveis. A lubrificação adequada reduz o atrito e o desgaste, permitindo que as máquinas operem de maneira mais suave e eficiente. Além disso, a lubrificação ajuda a dissipar o calor gerado pelo movimento das peças, contribuindo para a manutenção da temperatura ideal de operação.
Um aspecto importante do funcionamento de um sistema de lubrificação centralizada é o monitoramento e controle. Muitos sistemas modernos são equipados com sensores e dispositivos de monitoramento que permitem acompanhar o nível de lubrificante, a pressão do sistema e a temperatura. Esses dados são essenciais para garantir que o sistema esteja funcionando corretamente e para identificar problemas antes que se tornem críticos. O monitoramento em tempo real também permite que os operadores ajustem as configurações do sistema conforme necessário, garantindo uma lubrificação eficiente e eficaz.
Além disso, a manutenção do sistema de lubrificação centralizada é fundamental para seu funcionamento adequado. Isso inclui a verificação regular da bomba, das tubulações e dos distribuidores, bem como a substituição do lubrificante conforme necessário. A manutenção preventiva ajuda a evitar falhas no sistema e a garantir que as máquinas operem de maneira confiável e eficiente.
Os sistemas de lubrificação centralizada podem ser classificados em diferentes tipos, dependendo da aplicação e das necessidades específicas. Os sistemas de lubrificação por gravidade, por exemplo, utilizam a força da gravidade para distribuir o lubrificante, enquanto os sistemas de lubrificação por pressão utilizam bombas para forçar o lubrificante através das tubulações. Cada tipo de sistema tem suas próprias vantagens e desvantagens, e a escolha do sistema adequado depende das características da aplicação e das máquinas envolvidas.
Outro fator a ser considerado é a integração com outros sistemas. Muitos sistemas de lubrificação centralizada podem ser integrados a sistemas de automação industrial, permitindo um controle ainda mais preciso e eficiente. Isso pode incluir a programação de ciclos de lubrificação, a sincronização com o funcionamento das máquinas e a coleta de dados para análise de desempenho. A integração com sistemas de automação pode aumentar ainda mais a eficiência e a confiabilidade do processo de lubrificação.
Em resumo, um sistema de lubrificação centralizada funciona através de uma combinação de componentes que trabalham em conjunto para fornecer lubrificação eficiente e controlada a várias partes móveis de máquinas e equipamentos. A bomba de lubrificação, as tubulações, os distribuidores e os dispositivos de monitoramento são elementos essenciais que garantem o funcionamento adequado do sistema. Com a manutenção adequada e a integração com sistemas de automação, os sistemas de lubrificação centralizada podem melhorar significativamente a eficiência operacional e a durabilidade dos equipamentos industriais.
Tipos de Sistemas de Lubrificação Centralizada
Os sistemas de lubrificação centralizada são essenciais para garantir o funcionamento eficiente de máquinas e equipamentos em diversas indústrias. Eles permitem a distribuição controlada de lubrificantes, reduzindo o desgaste e aumentando a vida útil dos componentes. Existem diferentes tipos de sistemas de lubrificação centralizada, cada um com suas características e aplicações específicas. Neste artigo, vamos explorar os principais tipos de sistemas de lubrificação centralizada e suas vantagens.
Um dos tipos mais comuns de sistemas de lubrificação centralizada é o sistema de lubrificação por gravidade. Este sistema utiliza a força da gravidade para distribuir o lubrificante a partir de um reservatório localizado em uma posição elevada. O lubrificante flui naturalmente para os pontos de lubrificação através de tubulações. Este tipo de sistema é simples e econômico, sendo ideal para aplicações onde a pressão não é um fator crítico. No entanto, a gravidade pode limitar a distância que o lubrificante pode percorrer, o que pode ser uma desvantagem em máquinas maiores ou mais complexas.
Outro tipo popular é o sistema de lubrificação por pressão. Este sistema utiliza uma bomba para forçar o lubrificante através das tubulações até os pontos de lubrificação. Os sistemas de lubrificação por pressão são mais versáteis e podem ser usados em uma variedade de aplicações, desde máquinas pequenas até grandes equipamentos industriais. A pressão gerada pela bomba permite que o lubrificante alcance distâncias maiores e que seja distribuído de maneira mais uniforme. Além disso, esses sistemas podem ser equipados com dispositivos de monitoramento que garantem a pressão adequada e a quantidade de lubrificante aplicada.
Os sistemas de lubrificação por ponto único são uma variação dos sistemas de lubrificação por pressão. Eles são projetados para fornecer lubrificação a um único ponto de lubrificação, como um rolamento ou uma engrenagem. Esses sistemas são frequentemente utilizados em máquinas menores ou em aplicações onde a lubrificação precisa ser feita de forma precisa e controlada. A lubrificação por ponto único é eficiente e reduz o desperdício de lubrificante, pois aplica a quantidade exata necessária em cada ponto.
Os sistemas de lubrificação automática são outra categoria importante. Esses sistemas são projetados para operar de forma autônoma, realizando a lubrificação sem a necessidade de intervenção manual. Eles podem ser programados para lubrificar em intervalos regulares ou em resposta a condições específicas, como temperatura ou pressão. A automação da lubrificação reduz o risco de erro humano e garante que todas as partes móveis recebam a lubrificação necessária, aumentando a eficiência e a segurança das operações. Esses sistemas são particularmente úteis em ambientes industriais onde a lubrificação manual seria impraticável ou perigosa.
Além disso, existem os sistemas de lubrificação por spray, que utilizam um spray de lubrificante para aplicar o produto em superfícies específicas. O Lubrificante spray é ideal para áreas de difícil acesso ou para aplicações onde a lubrificação precisa ser feita de forma rápida e eficiente. Esses sistemas são frequentemente utilizados em manutenção e reparo, pois permitem uma aplicação precisa e controlada do lubrificante, minimizando o desperdício e a contaminação. O uso de lubrificantes em spray também facilita a aplicação em peças móveis que não podem ser facilmente desmontadas.
Os sistemas de lubrificação por neblina são uma opção inovadora que utiliza uma mistura de ar e lubrificante para criar uma névoa que é distribuída nas partes móveis. Esse tipo de sistema é ideal para aplicações onde a lubrificação precisa ser feita de forma contínua e em ambientes onde a contaminação deve ser minimizada. A névoa de lubrificante penetra em áreas de difícil acesso e proporciona uma cobertura uniforme, reduzindo o atrito e o desgaste. Os sistemas de lubrificação por neblina são frequentemente utilizados em indústrias de alta precisão, como a fabricação de componentes eletrônicos e mecânicos.
Por fim, os sistemas de lubrificação hidráulica são utilizados em aplicações que exigem lubrificação e controle de movimento simultaneamente. Esses sistemas utilizam fluidos hidráulicos para lubrificar e operar componentes, como cilindros e motores. A lubrificação hidráulica é comum em equipamentos pesados, como escavadeiras e guindastes, onde a eficiência e a precisão são cruciais. Esses sistemas são projetados para suportar altas pressões e temperaturas, garantindo um desempenho confiável em condições adversas.
Em resumo, existem diversos tipos de sistemas de lubrificação centralizada, cada um com suas características e aplicações específicas. Desde sistemas de gravidade e pressão até lubrificação automática e por spray, cada tipo oferece vantagens que podem ser aproveitadas em diferentes contextos industriais. A escolha do sistema adequado depende das necessidades específicas de cada aplicação, e a implementação de um sistema de lubrificação centralizada pode resultar em melhorias significativas na eficiência operacional e na durabilidade dos equipamentos.
Manutenção e Cuidados com Sistemas de Lubrificação Centralizada
A manutenção adequada dos sistemas de lubrificação centralizada é fundamental para garantir seu funcionamento eficiente e prolongar a vida útil dos equipamentos. Esses sistemas desempenham um papel crucial na redução do desgaste e na prevenção de falhas mecânicas, e sua eficácia depende de cuidados regulares e de uma abordagem proativa. Neste artigo, abordaremos as melhores práticas de manutenção e cuidados que devem ser adotados para assegurar o desempenho ideal dos sistemas de lubrificação centralizada.
Um dos primeiros passos na manutenção de um sistema de lubrificação centralizada é a verificação regular dos níveis de lubrificante. É essencial garantir que o reservatório de lubrificante esteja sempre cheio e que não haja vazamentos nas tubulações ou conexões. A falta de lubrificante pode levar a um aumento do atrito e do desgaste das peças, resultando em falhas e paradas não programadas. Portanto, recomenda-se realizar inspeções visuais frequentes e, se necessário, reabastecer o lubrificante de acordo com as especificações do fabricante.
Além da verificação dos níveis de lubrificante, é importante monitorar a qualidade do lubrificante utilizado. Com o tempo, o lubrificante pode se degradar devido à contaminação, oxidação ou à presença de partículas indesejadas. A utilização de lubrificantes de alta qualidade, como a graxa branca alimentícia, pode ajudar a minimizar esses problemas. Realizar análises periódicas do lubrificante, como testes de viscosidade e contaminação, pode fornecer informações valiosas sobre sua condição e ajudar a determinar quando é necessário substituí-lo.
Outro aspecto importante da manutenção é a limpeza das tubulações e componentes do sistema. A sujeira e os contaminantes podem se acumular nas tubulações, distribuidores e pontos de lubrificação, comprometendo a eficiência do sistema. Recomenda-se realizar uma limpeza regular das tubulações e dos componentes, utilizando produtos adequados que não danifiquem o sistema. A limpeza deve ser feita de acordo com as orientações do fabricante e pode incluir a remoção de resíduos, a desobstrução de filtros e a verificação de válvulas.
A inspeção das bombas de lubrificação é outro ponto crucial na manutenção de sistemas de lubrificação centralizada. As bombas são responsáveis por pressurizar e distribuir o lubrificante, e qualquer falha nesse componente pode comprometer todo o sistema. É importante verificar o funcionamento da bomba, observando se há ruídos anormais, vibrações ou vazamentos. Caso sejam identificados problemas, a bomba deve ser reparada ou substituída imediatamente para evitar danos maiores.
Além disso, a calibração dos distribuidores é uma parte essencial da manutenção. Os distribuidores são responsáveis por dividir o fluxo de lubrificante entre os diferentes pontos de lubrificação, e uma calibração inadequada pode resultar em uma distribuição desigual. É recomendável verificar periodicamente a configuração dos distribuidores e ajustá-los conforme necessário, garantindo que cada ponto receba a quantidade correta de lubrificante. Isso é especialmente importante em sistemas que operam em condições variáveis ou que utilizam diferentes tipos de lubrificantes.
Outro cuidado importante é a verificação dos sensores e dispositivos de monitoramento que podem estar integrados ao sistema. Esses dispositivos são essenciais para garantir que o sistema esteja operando dentro dos parâmetros ideais. A calibração e a manutenção dos sensores devem ser realizadas regularmente, e qualquer falha deve ser corrigida imediatamente. A monitorização em tempo real permite que os operadores identifiquem problemas antes que se tornem críticos, aumentando a confiabilidade do sistema.
Além das práticas de manutenção mencionadas, é fundamental treinar a equipe responsável pela operação e manutenção do sistema. O conhecimento adequado sobre o funcionamento do sistema de lubrificação centralizada e as melhores práticas de manutenção pode fazer uma grande diferença na eficiência e na durabilidade do equipamento. Treinamentos regulares e atualizações sobre novas tecnologias e procedimentos podem ajudar a equipe a se manter informada e preparada para lidar com qualquer situação.
Por fim, é importante documentar todas as atividades de manutenção realizadas no sistema. Manter um registro detalhado das inspeções, limpezas, substituições de lubrificante e reparos pode ajudar a identificar padrões e tendências ao longo do tempo. Essa documentação é valiosa para a análise de desempenho do sistema e pode ser útil para futuras manutenções e para a tomada de decisões sobre melhorias e upgrades.
Em resumo, a manutenção e os cuidados com sistemas de lubrificação centralizada são essenciais para garantir seu funcionamento eficiente e prolongar a vida útil dos equipamentos. A verificação regular dos níveis e da qualidade do lubrificante, a limpeza das tubulações, a inspeção das bombas e a calibração dos distribuidores são práticas fundamentais que devem ser adotadas. Além disso, o treinamento da equipe e a documentação das atividades de manutenção são aspectos importantes que contribuem para a eficácia do sistema. Com uma abordagem proativa e cuidadosa, é possível maximizar os benefícios dos sistemas de lubrificação centralizada e garantir operações industriais mais seguras e eficientes.
Em conclusão, os sistemas de lubrificação centralizada são fundamentais para o desempenho e a longevidade de máquinas e equipamentos industriais. Através da distribuição eficiente de lubrificantes, esses sistemas não apenas protegem as partes móveis, mas também contribuem para a redução de custos operacionais e a minimização de paradas não programadas. Compreender as vantagens, o funcionamento e os diferentes tipos de sistemas de lubrificação centralizada, assim como adotar práticas de manutenção adequadas, é essencial para maximizar os benefícios e garantir um ambiente de trabalho mais seguro e produtivo. Investir em um sistema de lubrificação centralizada é, portanto, uma decisão estratégica que pode resultar em melhorias significativas na eficiência operacional e na durabilidade dos equipamentos.