Como Funciona um Sistema de Lubrificação Automático e Seus Benefícios
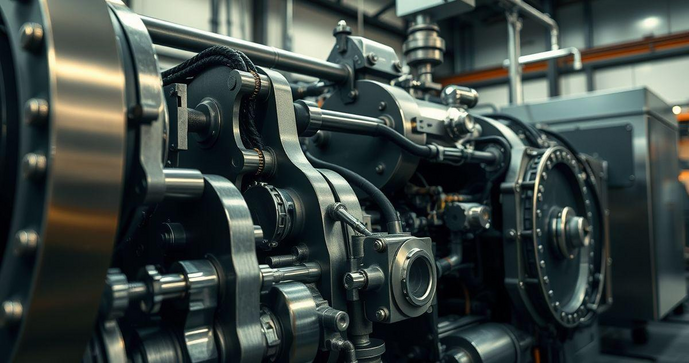
Por: Victória - 24 de Março de 2025
Vantagens de um Sistema de Lubrificação Automático
A adoção de um sistema de lubrificação automático traz diversas vantagens que podem impactar positivamente a operação de máquinas e equipamentos. Abaixo, exploraremos as principais benesses que essa tecnologia oferece.
Eficiência Aumentada: Um sistema de lubrificação automático permite a distribuição precisa de lubrificante em intervalos regulares, evitando a sobrecarga em algumas áreas e garantindo que todas as partes móveis recebam a quantidade adequada de lubrificante. Isso resulta em um funcionamento mais suave e eficiente.
Redução de Desgaste: A lubrificação adequada minimiza o atrito entre componentes, reduzindo assim o desgaste e prolongando a vida útil dos equipamentos. Com menos fricção, as peças se desgastam menos e apresentam uma performance superior.
Menor Intervenção Manual: A automação do processo de lubrificação diminui a necessidade de inspeções e manutenções manuais constantes. Isso não apenas reduz o tempo de inatividade, mas também permite que os operadores se concentrem em outras atividades produtivas.
Consciência Ambiental: Sistemas automáticos podem ser projetados para usar lubrificantes de forma mais eficiente, reduzindo o desperdício de materiais e os impactos ambientais negativos associados ao manuseio e descarte de lubrificantes.
Detecção de Falhas: Muitos sistemas de lubrificação automática vêm equipados com sensores que monitoram o nível do lubrificante e a condição das peças, alertando para possíveis falhas antes que elas se tornem críticas. Isso permite ações corretivas rápidas e eficazes.
Economia de Custos: Ao reduzir o desgaste, a necessidade de manutenção e as quebras inesperadas, um sistema de lubrificação automático pode resultar em uma economia significativa a longo prazo. Essa tecnologia não apenas protege o investimento inicial em equipamentos, mas também contribui para uma operação mais econômica.
As vantagens de um sistema de lubrificação automático são claras, abrangendo desde a eficiência e a redução de custos até a melhoria na vida útil dos equipamentos. Essas características tornam essa tecnologia uma escolha inteligente para indústrias que buscam maximizar sua produtividade e minimizar falhas operacionais.
Componentes Essenciais do Sistema
Um sistema de lubrificação automático é composto por diversos componentes que trabalham em conjunto para garantir um funcionamento eficiente. Conhecer esses elementos é fundamental para entender como o sistema opera e para a manutenção adequada.
Tanque de Lubrificante: Este componente armazena o lubrificante que será distribuído. O tamanho do tanque pode variar dependendo das necessidades do sistema, e sua capacidade deve ser dimensionada de acordo com a demanda da operação.
Bomba de Lubrificação: A bomba é responsável por mover o lubrificante do tanque para os pontos de lubrificação. Existem diferentes tipos de bombas, como as pneumáticas e elétricas, cada uma com características que se adaptam a diferentes aplicações e requisitos.
Distribuidor: O distribuidor é um dispositivo que controla a quantidade de lubrificante que vai para cada ponto de lubrificação. Ele pode ser ajustado para diferentes fluxos, permitindo uma distribuição precisa conforme as necessidades de cada parte móvel.
Tubulações e Conexões: As tubulações transportam o lubrificante da bomba aos pontos de aplicação. É essencial que essas tubulações sejam adequadas ao tipo de lubrificante utilizado e que estejam livre de obstruções ou vazamentos.
Sensores de Nível: Esses dispositivos monitoram o nível de lubrificante no tanque, garantindo que não ocorra falta de lubrificante durante a operação. Podem também acionar alarmes ou sinais para quando for necessário reabastecer o sistema.
Controles de Automação: A parte eletrônica do sistema, que pode incluir painéis de controle e programação, permite que o processo de lubrificação seja automatizado. Esses controles ajudam a programar intervalos de lubrificação e a monitorar o funcionamento do sistema.
Cada um desses componentes desempenha um papel vital na operação geral do sistema de lubrificação automático. A compreensão desses elementos é fundamental não apenas para a instalação, mas também para a manutenção e otimização do sistema, garantindo sua eficácia a longo prazo.
Como Funciona o Processo de Lubrificação
O funcionamento de um sistema de lubrificação automático envolve um processo metódico que assegura a distribuição adequada de lubricantes a diversas partes móveis. A seguir, detalharemos as etapas principais desse processo.
Inicialização do Sistema: O processo de lubrificação começa com a ativação do sistema, que pode ser programado para iniciar automaticamente em intervalos específicos ou acionado manualmente conforme a necessidade. Ao ser iniciado, a bomba de lubrificação se prepara para puxar o lubrificante do tanque.
Transporte do Lubrificante: Assim que a bomba é ativada, o lubrificante é pressurizado e transportado através das tubulações até o distribuidor. Essa fase é crucial, pois garante que o lubrificante chegue aos pontos de aplicação sem interrupções.
Distribuição Controlada: O distribuidor controla a quantidade de lubrificante que será enviada a cada ponto de lubrificação. Essa distribuição é ajustada conforme a necessidade de cada componente. Sensores podem garantir que o fluxo esteja dentro das especificações ideais, maximizando a eficiência.
Aplicação no Equipamento: Após a distribuição, o lubrificante atinge os pontos de aplicação, como rolamentos, engrenagens ou qualquer outro componente que requer lubrificação. Aqui, o lubrificante atua na redução do atrito e no desgaste, proporcionando um funcionamento suave.
Retorno do Lubrificante Desperdiçado: Em muitos sistemas, o lubrificante que não é utilizado retorna ao tanque para ser reutilizado. Esse ciclo ajuda a economizar recursos e garante que o sistema opere de forma sustentável.
Monitoramento e Ajustes: Sensores de nível e pressão monitoram o sistema continuamente, garantindo que não haja falhas no processo. Se necessário, ajustes podem ser feitos para garantir que a lubrificação seja sempre adequada e eficiente.
O processo de lubrificação em um sistema automático é fundamental para o desempenho e a longevidade dos maquinários. A automatização desses processos não apenas otimiza a operação, mas também ajuda a garantir que cada componente receba a atenção necessária, resultando em uma performance melhorada.
Aplicações Comuns em Indústrias
Os sistemas de lubrificação automáticos têm aplicações diversas nas indústrias, desempenhando um papel crucial na maximização da eficiência e na minimização do desgaste em equipamentos. A seguir, serão apresentadas algumas das principais indústrias que se beneficiam dessa tecnologia.
Indústria Automotiva: Na fabricação de veículos, os sistemas de lubrificação automática são utilizados em linhas de montagem e em maquinas de usinagem. A lubrificação eficiente assegura que as partes móveis de motores e equipamentos de produção operem corretamente, aumentando a qualidade e a produtividade.
Setor Metalúrgico: Máquinas de corte e moldagem de metais requerem lubrificação contínua para evitar o superaquecimento e o desgaste das ferramentas. Sistemas automáticos garantem que esses processos sejam realizados sem atrasos e com precisão, contribuindo para a eficiência geral das operações.
Indústria Alimentícia: Na produção de alimentos, a higiene é essencial. Sistemas de lubrificação automáticos que utilizam lubrificantes apropriados e seguros para o contato com alimentos são utilizados em máquinas de envase, transporte e processamento. Isso assegura não apenas a eficiência, mas também a conformidade com as normas de segurança alimentar.
Setor de Energia: Em usinas de energia, tanto renováveis quanto fósseis, a lubrificação automática garante que as turbinas e os sistemas de transporte de carvão ou biomassa operem de forma confiável. Isso é fundamental para manter a continuidade da produção de energia e evitar paradas inesperadas.
Indústria de Papel e Celulose: Maquinários utilizados na fabricação de papel e celulose frequentemente operam em altas velocidades e sob condições severas. A lubrificação automática ajuda a reduzir o atrito e a temperatura, aumentando a eficiência e a confiabilidade dos equipamentos.
Setor Químico: Equipamentos como reatores e misturadores requerem um excelente controle de lubrificação para garantir operações seguras e eficazes. Sistemas automáticos são usados para garantir que todas as partes móveis sejam lubrificadas adequadamente, reduzindo assim o risco de falhas.
Os sistemas de lubrificação automática são fundamentais em uma variedade de indústrias, assegurando eficiência, segurança e longevidade dos equipamentos. Sua versatilidade e adaptabilidade os tornam uma escolha valiosa para qualquer operação industrial que deseje otimizar processos.
Manutenção e Cuidados Necessários
A manutenção adequada de um sistema de lubrificação automático é essencial para garantir seu funcionamento eficiente e prolongar sua vida útil. A seguir, descreveremos os cuidados e procedimentos necessários para a manutenção eficaz desse sistema.
Verificação Regular dos Componentes: Inspecionar frequentemente os principais componentes, como bombas, distribuidores e tubulações, é fundamental. Isso ajuda a identificar desgastes ou danos precoces, permitindo que reparos sejam feitos antes que se tornem problemas maiores.
Limpeza do Sistema: A poeira, resíduos de lubrificantes e outras impurezas podem obstruir os componentes do sistema. Realizar limpeza regular nas tubulações e nos sensores ajuda a assegurar que o fluido seja transportado de forma adequada e que o sistema funcione sem interrupções.
Troca de Lubrificante: Se o sistema não é projetado para reutilizar o lubrificante, é crucial trocar o fluido periodicamente de acordo com as recomendações do fabricante. Lubrificantes desgastados podem comprometer a eficácia do sistema e aumentar o risco de falhas.
Calibração de Sensores e Distribuidores: Sensores que controlam o nível e a pressão do lubrificante devem ser calibrados regularmente para garantir medidas precisas. Verificar as configurações dos distribuidores também assegura que a quantidade correta de lubrificante esteja sendo aplicada em cada ponto.
Monitoramento Contínuo: Utilizar tecnologia para monitorar o funcionamento do sistema em tempo real pode ajudar a identificar problemas rapidamente. Sistemas de telemetria e software de gestão permitem que os operadores acompanhem o desempenho do sistema e recebam alertas sobre qualquer anomalia.
Treinamento da Equipe: Garantir que a equipe responsável pela manutenção e operação do sistema esteja bem treinada é um fator crítico. O entendimento sobre como o sistema funciona, além das práticas de manutenção, pode prevenir erros e aumentar a eficiência operacional.
A manutenção e os cuidados necessários para um sistema de lubrificação automático são essenciais para maximizar sua durabilidade e eficiência. Investir tempo e recursos na manutenção regular garante que o sistema opere de maneira confiável e eficaz, evitando paradas e danos dispendiosos.
Comparação com Sistemas Manuais de Lubrificação
A comparação entre sistemas automáticos e manuais de lubrificação é essencial para entender as vantagens e desvantagens de cada abordagem. Essa análise ajuda indústrias a decidirem qual sistema melhor atende suas necessidades operacionais.
Eficiência: Sistemas automáticos oferecem lubrificação constante em intervalos programados, garantindo que todas as partes sejam atendidas adequadamente. Em contraste, os sistemas manuais dependem da intervenção humana, o que pode resultar em intervalos de lubrificação irregulares e, consequentemente, em desgaste prematuro das máquinas.
Consistência: A automação proporciona uma distribuição de lubrificante uniforme e precisa em todos os pontos de lubrificação, enquanto nos sistemas manuais a lubrificação pode ser inconsistente, devido a variações na metodologia de aplicação de diferentes operadores.
Custo de Mão de Obra: Sistemas manuais de lubrificação geralmente requerem mais tempo e mão de obra, resultando em custos adicionais para as empresas. Por outro lado, sistemas automáticos reduzem a necessidade de trabalho manual, permitindo que a equipe se concentre em outras tarefas produtivas.
Segurança: O uso de sistemas automáticos minimiza a necessidade de trabalhadores acessarem áreas potencialmente perigosas para lubrificar máquinas. Isso reduz o risco de acidentes de trabalho, enquanto em sistemas manuais, é comum que os operadores se expõem a perigos ao realizar a lubrificação perto de partes móveis.
Monitoramento: Sistemas automáticos costumam incluir monitoramento remoto e feedback em tempo real, o que permite detecção imediata de problemas. Em sistemas manuais, a identificação de falhas pode levar mais tempo, resultando em potenciais paradas inesperadas e perdas operacionais.
Custo Inicial: Embora a implementação de um sistema automático possa exigir um investimento inicial maior, o retorno sobre esse investimento é geralmente observado ao longo do tempo, devido à redução de custos de manutenção e ao aumento da eficiência. Em comparação, sistemas manuais têm custos iniciais mais baixos, mas podem resultar em maiores despesas a longo prazo devido à manutenção frequente e possíveis quebras de equipamento.
Ao comparar sistemas automáticos com manuais de lubrificação, é evidente que a automação proporciona benefícios significativos em termos de eficiência, consistência e segurança. Embora exijam um investimento inicial mais alto, os sistemas automáticos desenvolvem um retorno favorável ao longo do tempo, justificando sua adoção em ambientes industriais.
A implementação de um sistema de lubrificação automático traz inúmeras vantagens para as indústrias, incluindo eficiência aprimorada, redução de custos, maior segurança e prolongamento da vida útil dos equipamentos.
Com a automação, as empresas são capazes de proporcionar uma lubrificação uniforme e contínua, minimizando o desgaste das partes mecânicas e evitando falhas operacionais.
A comparação com sistemas manuais mostra que, apesar do investimento inicial, os sistemas automáticos oferecem um retorno significativo em economia e produtividade ao longo do tempo.
Portanto, adotar essa tecnologia é um passo decisivo para a modernização e otimização das operações industriais, garantindo não apenas a segurança, mas também a competitividade no mercado.