Como Escolher o Melhor Sistema de Lubrificação para Correntes
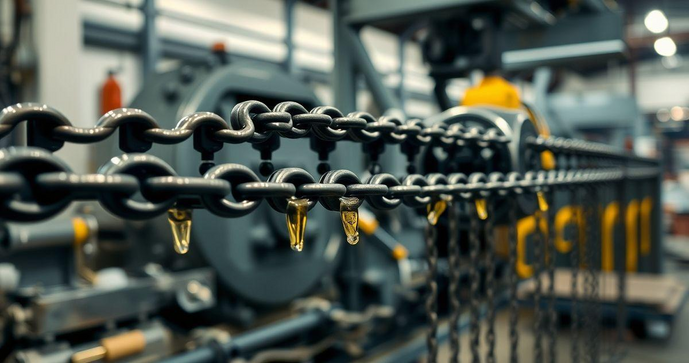
Por: Victória - 20 de Março de 2025
Importância da Lubrificação em Sistemas de Correntes
A lubrificação adequada em sistemas de correntes desempenha um papel crucial na operação eficiente de maquinários. Sem um sistema de lubrificação eficaz, as correntes podem sofrer desgaste acelerado, resultando em falhas e interrupções da produção. Isso não apenas afeta o desempenho do equipamento, mas também pode causar danos colaterais a outros componentes do sistema.
Um dos principais benefícios da lubrificação é a redução do atrito. Quando as correntes estão devidamente lubrificadas, o atrito entre os elos e os rolamentos é significativamente reduzido, o que minimiza o calor gerado durante a operação. Isso aumenta a eficiência do sistema, permitindo um funcionamento mais suave e prolongando a vida útil dos componentes.
Além disso, a lubrificação ajuda a prevenir a corrosão. As correntes expostas a ambientes úmidos ou corrosivos estão em risco de deterioração. Um bom sistema de lubrificação não só atende à necessidade de eficiência, mas também protege as correntes contra agentes corrosivos, aumentando sua resistência e durabilidade.
Outro ponto importante é que um sistema de lubrificação bem projetado pode contribuir para a segurança operacional. Correntes devidamente mantidas são menos propensas a falhas, o que reduz o risco de acidentes em ambientes de trabalho. Além disso, isso garante que os equipamentos operem conforme esperado, evitando paradas inesperadas que podem gerar perdas financeiras.
Em resumo, a importância da lubrificação em sistemas de correntes não pode ser subestimada. Investir em um sistema de lubrificação apropriado é fundamental para garantir a eficiência, durabilidade e segurança de equipamentos que utilizam correntes.
Tipos de Sistemas de Lubrificação Disponíveis
Existem diversos tipos de sistemas de lubrificação disponíveis no mercado, cada um projetado para atender a necessidades específicas de operação e manutenção de correntes. A escolha do sistema ideal pode impactar diretamente a eficiência e a durabilidade dos equipamentos. A seguir, abordaremos os principais tipos de sistemas de lubrificação:
1. Lubrificação Manual: Este é o método mais simples e tradicional, onde a aplicação do lubrificante é feita manualmente pelo operador. Embora seja uma abordagem econômica, depende da regularidade e da atenção do operador para garantir que as correntes sejam lubrificadas com a frequência necessária.
2. Lubrificação Automática por Ponto: Este sistema utiliza unidades de lubrificação que aplicam quantidades específicas de lubrificante em intervalos programados. É uma solução que reduz o trabalho manual, garantindo que as correntes sejam mantidas em ótimas condições de maneira regular.
3. Lubrificação por Spray: Este método envolve o uso de um dispositivo que atomiza o lubrificante, garantindo uma distribuição uniforme sobre a superfície da corrente. É ideal para operações em ambientes difíceis, onde a aplicação manual pode ser impraticável.
4. Lubrificação por Deslocamento: Este sistema, geralmente, utiliza tubulações e bombas para distribuir o lubrificante em locais de difícil acesso. É muito utilizado em aplicações industriais pesadas onde as correntes operam sob altas cargas e exigem um fornecimento constante de lubrificação.
5. Lubrificação por Banho ou Imersão: Ao invés de aplicar o lubrificante diretamente, esse sistema envolve a imersão das correntes em um reservatório de lubrificante. Isso proporciona uma lubrificação completa e contínua, sendo utilizado em aplicações onde a contaminação por poeira e sujeira é uma preocupação.
6. Lubrificação com Óleo Sintético: Este tipo de lubrificação utiliza óleos sintéticos que oferecem maior resistência à temperatura e melhor proteção contra desgaste. É ideal para sistemas que operam em condições extremas, proporcionando uma vida útil mais longa para as correntes.
Em resumo, a escolha do tipo de sistema de lubrificação deve levar em conta o ambiente de operação, a frequência de uso, e as características específicas das correntes. Cada sistema oferece vantagens e desvantagens, e uma boa análise pode garantir a eficiência e a durabilidade do equipamento.
Critérios para Escolher o Sistema Ideal
A escolha do sistema de lubrificação ideal para correntes envolve a consideração de vários critérios, que podem afetar diretamente a eficiência e a durabilidade do equipamento. Avaliar esses fatores é fundamental para garantir que o sistema atenda às necessidades específicas da operação. A seguir, apresentamos os principais critérios a serem levados em conta:
1. Tipo de Trabalho: O ambiente em que as correntes operam é crucial na escolha do sistema de lubrificação. Se as correntes estiverem expostas a altas temperaturas, umidade ou contaminantes, um sistema que ofereça proteção adicional e resistência será necessário, como a lubrificação por óleo sintético.
2. Frequência de Operação: Para sistemas que funcionam com alta frequência, a necessidade de lubrificação regular se torna ainda mais importante. Sistemas automáticos, como os de lubrificação por ponto ou deslocamento, podem ser mais adequados para garantir que a lubrificação ocorra nos momentos certos, sem depender da atenção constante do operador.
3. Acessibilidade: É importante considerar a facilidade de acesso aos componentes do sistema de lubrificação. Em ambientes de difícil acesso, métodos automáticos e por spray podem ser mais eficazes do que a lubrificação manual, que pode se tornar um desafio em operações complexas.
4. Custo-Benefício: A análise do custo de instalação e manutenção do sistema de lubrificação deve ser feita considerando os benefícios a longo prazo. Sistemas mais complexos podem demandar investimentos iniciais mais altos, mas podem resultar em economias significativas em manutenção e operação no futuro.
5. Compatibilidade com o Lubrificante: Nem todos os sistemas de lubrificação são adequados para todos os tipos de lubrificantes. É fundamental verificar as especificações do lubrificante a ser utilizado e garantir que o sistema escolhido seja compatível, evitando assim problemas de desempenho ou falhas nos componentes.
6. Facilidade de Manutenção: Um sistema que requer baixa manutenção pode ser preferível, especialmente em ambientes onde a mão de obra é escassa. É importante escolher um sistema que permita manutenção simples e não represente um ônus para a operação diária.
Em resumo, a escolha do sistema de lubrificação ideal deve ser fundamentada em uma avaliação cuidadosa desses critérios. Considerando o ambiente de trabalho, as características das correntes e os objetivos de operação, é possível garantir uma lubrificação eficaz que promova a durabilidade e a eficiência do sistema.
Benefícios da Automação na Lubrificação
A automação na lubrificação de correntes traz uma série de benefícios significativos que podem transformar a eficiência e a segurança operacional de maquinários. A seguir, vamos explorar as principais vantagens de implementar sistemas automáticos de lubrificação:
1. Consistência e Regularidade: Sistemas automatizados garantem que a lubrificação ocorra em intervalos regulares e programados, eliminando a possibilidade de esquecimento ou atrasos que podem ocorrer com a lubrificação manual. Isso resulta em uma manutenção mais constante e eficaz.
2. Redução de Paradas Não Planejadas: Com a automação, a lubrificação é realizada sem a necessidade de interromper as operações do maquinário. Isso ajuda a evitar paradas não planejadas, aumentando a produtividade e a eficiência geral do sistema.
3. Economia de Tempo e Mão de Obra: A automação reduz a necessidade de intervenções manuais constantes. Isso libera os operadores para se concentrarem em outras tarefas mais críticas e diminui os custos relacionados à mão de obra, aumentando a eficiência operacional.
4. Precisão na Aplicação: Sistemas automáticos aplicam a quantidade exata de lubrificante necessária, de acordo com as especificações do fabricante. Isso minimiza o desperdício de lubrificante e assegura que as correntes recebam a proteção adequada sem o excesso que poderia causar acúmulo e sujeira.
5. Melhoria na Segurança: A automação reduz a necessidade de trabalhadores operarem em áreas perigosas durante as aplicações de lubrificante. Os sistemas podem ser instalados em lugares de difícil acesso, minimizando risco de acidentes e expondo menos pessoas a ambientes potencialmente perigosos.
6. Monitoramento em Tempo Real: Muitos sistemas automatizados permitem o monitoramento em tempo real dos níveis de lubrificação e das condições de operação. Isso possibilita detectar problemas antes que se tornem críticos, permitindo intervenções proativas e manutenção preditiva.
7. Aumento da Vida Útil dos Componentes: Com uma lubrificação adequada e consistente, os componentes do maquinário, incluindo as correntes, têm uma vida útil significativamente prolongada. Isso se traduz em menores custos de reposição e manutenção ao longo do tempo.
Em síntese, a automação na lubrificação de correntes não só melhora a eficiência e a durabilidade dos sistemas, mas também contribui para a segurança e a economia operacional, tornando-se uma escolha cada vez mais popular nas indústrias modernas.
Manutenção e Cuidados com o Sistema de Lubrificação
A manutenção adequada do sistema de lubrificação é fundamental para garantir que ele funcione de forma eficiente e prolongue a vida útil das correntes e dos componentes do maquinário. Aqui estão as principais práticas e cuidados a serem adotados:
1. Inspeções Regulares: Realizar inspeções periódicas no sistema de lubrificação é essencial para identificar problemas potenciais antes que se tornem sérios. Verifique se há vazamentos, danos aos componentes e adequação das conexões.
2. Limpeza dos Componentes: A sujeira e os contaminantes podem afetar o funcionamento do sistema de lubrificação. É importante manter os componentes limpos, removendo detritos que possam obstruir os caminhos de lubrificação ou afetar a aplicação do lubrificante.
3. Verificação do Lubrificante: O tipo e a qualidade do lubrificante utilizado devem ser periodicamente verificados. Substitua lubrificantes que tenham perdido suas propriedades ou que estejam contaminados para garantir o desempenho ideal do sistema.
4. Ajustes de Programação: Para sistemas automáticos, revise e ajuste a programação regularmente para garantir que a lubrificação ocorra nos níveis e intervalos adequados. Isso vai ajudar a evitar tanto a sublubrificação quanto a sobreelevação do lubrificante.
5. Monitoramento dos Níveis de Lubrificante: Certifique-se de que os reservatórios de lubrificante estejam sempre nos níveis adequados. A falta de lubrificante pode levar a um desgaste prematuro das correntes e outros componentes do sistema.
6. Treinamento de Equipe: A equipe que opera e mantém o sistema de lubrificação deve receber treinamento adequado sobre a importância da manutenção e sobre como realizar as tarefas necessárias. Isso garante que todos estejam cientes dos procedimentos corretos e das melhores práticas.
7. Documentação de Manutenção: Mantenha registros detalhados de todas as atividades de manutenção realizadas, incluindo inspeções, limpezas e substituições de lubrificante. Esses registros são úteis para futuras análises e podem ajudar a identificar tendências ou problemas recorrentes.
Em resumo, adotar práticas rigorosas de manutenção e cuidados com o sistema de lubrificação é essencial para garantir sua eficácia e prolongar a vida útil das correntes e dos equipamentos associados. A manutenção proativa previne falhas, melhora a eficiência do sistema e garante um desempenho consistente ao longo do tempo.
Dicas para Aumentar a Vida Útil das Correntes
Aumentar a vida útil das correntes em sistemas de lubrificação é fundamental para reduzir custos e garantir a eficiência operacional. Aqui estão algumas dicas práticas que podem ajudar a prolongar a durabilidade das correntes:
1. Realize Lubrificações Regulares: A lubrificação deve ser feita regularmente de acordo com as recomendações do fabricante. Correntes bem lubrificadas têm menos atrito, o que reduz o desgaste e previne falhas precoces.
2. Mantenha a Limpeza: A sujeira, poeira e outros contaminantes podem se acumular nas correntes e danificá-las. Realize limpezas periódicas para remover detritos e manter as correntes em condições ideais.
3. Verifique o Alinhamento: Correntes que não estão adequadamente alinhadas podem sofrer tensões desnecessárias, levando ao desgaste prematuro. Realize inspeções regulares para garantir que tudo esteja bem alinhado.
4. Use Lubrificantes de Qualidade: Escolha lubrificantes de alta qualidade que sejam apropriados para o tipo de operação das correntes. Isso garante proteção adequada contra desgaste e corrosão.
5. Evite Sobrecarga: Não exagere na carga suportada pelas correntes. Verifique as especificações do fabricante para saber a capacidade de carga adequada e evite operações que possam sobrecarregar as correntes.
6. Realize Manutenção Preventiva: Adote um plano de manutenção preventiva que inclua inspeções regulares, lubrificação, e substituição de peças desgastadas. Isso vai ajudar a identificar e corrigir problemas antes que eles se agravem.
7. Proteja Contra Corrosão: Se as correntes estiverem expostas a ambientes úmidos ou corrosivos, utilize revestimentos protetores ou selecione correntes com tratamento anticorrosivo. Isso ajuda a prolongar a vida útil ao impedir a degradação.
8. Armazenamento Adequado: Quando não estiverem em uso, armazene as correntes em locais secos e limpos, evitando a exposição a condições ambientais adversas que possam causar danos.
Seguindo estas dicas, é possível aumentar a vida útil das correntes e garantir um funcionamento mais eficiente e duradouro dos maquinários. A adoção de práticas de manutenção eficazes é um investimento que traz resultados positivos a longo prazo.
A manutenção e a escolha do sistema de lubrificação adequado para correntes são fatores essenciais que influenciam diretamente a eficiência e a durabilidade dos equipamentos.
Compreender a importância da lubrificação, conhecer os diferentes tipos de sistemas disponíveis, e seguir práticas recomendadas de manutenção pode resultar em menos paradas inesperadas e custos reduzidos ao longo do tempo.
Além disso, a automação na lubrificação oferece vantagens significativas, como consistência e precisão, contribuindo para a proteção das correntes e aumentando sua vida útil.
Seguir as dicas apresentadas para cuidados e manutenção garante que as correntes funcionem de forma ideal, maximizando seu desempenho.
Em resumo, a implementação de um sistema de lubrificação eficaz e a adoção de práticas de manutenção rigorosas são investimentos estratégicos que beneficiam não apenas a durabilidade das correntes, mas também toda a eficiência operacional do maquinário.